In the high-stakes realm of military and defense, there’s no margin for error when it comes to the components powering critical systems. From advanced missile guidance to battlefield communication systems, every part must function flawlessly in even the most extreme conditions.
For industries where lives depend on reliability, performance, and resilience, precision is not a luxury — it’s a necessity. With stringent regulatory requirements like MIL-SPEC, AS9100, and ITAR, contractors in the defense industry must partner with manufacturers capable of delivering consistent, high-performance metal components. That’s where Photofabrication Engineering, Inc. (PEI) comes in.
As a leader in precision metal manufacturing, PEI leverages decades of experience and the specialized skills of our Engineering, Manufacturing, and Quality Assurance teams to produce ultra-reliable, military-grade parts. Using our proven photochemical etching process, we deliver components that meet the highest standards of accuracy, strength, and compliance.
In this article, we explore the critical role of precision metal parts in military applications, the challenges of defense manufacturing, the benefits of PCE, and why PEI is the trusted partner for mission-critical components.
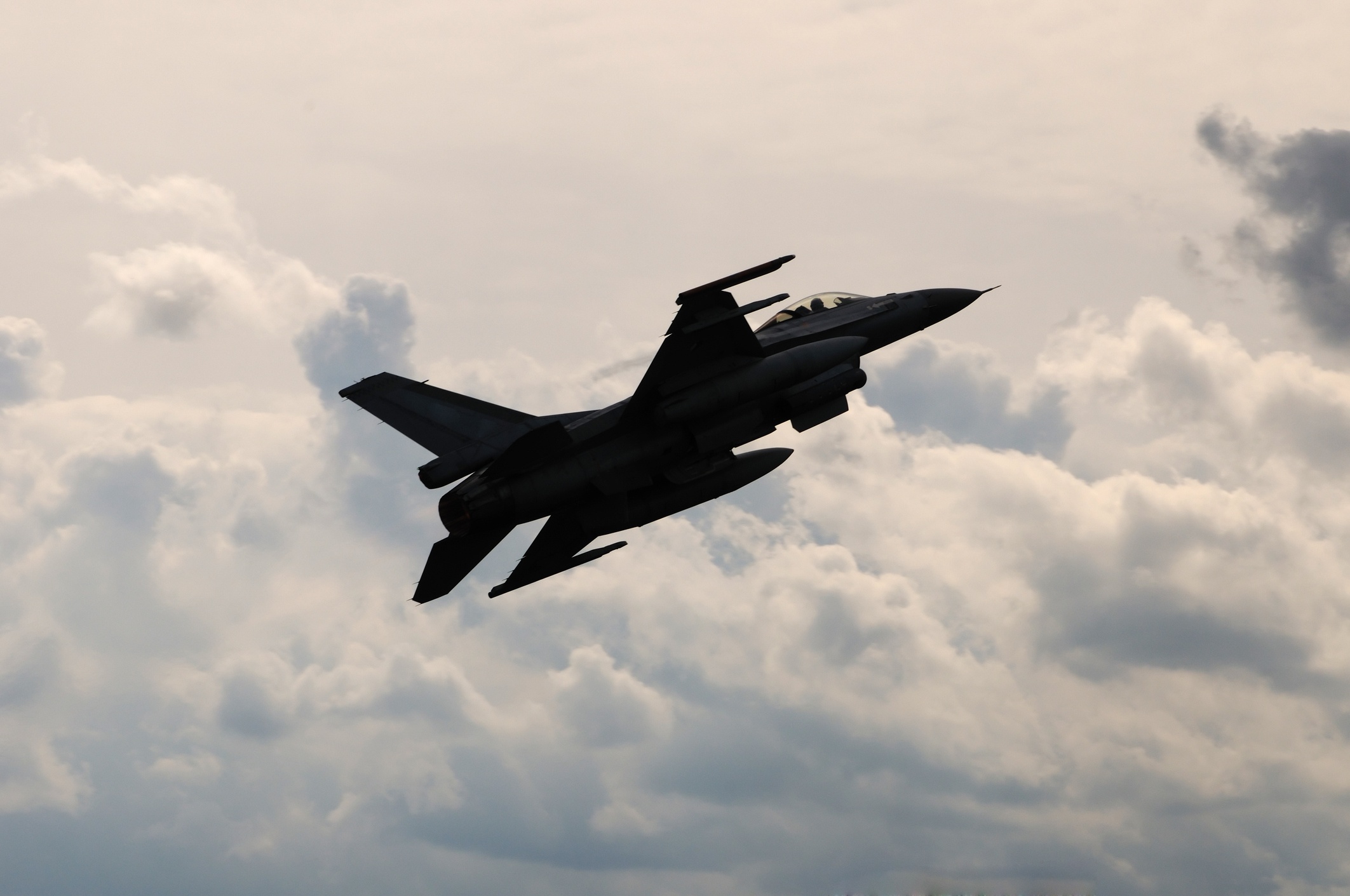
The Importance of Precision Metal Parts in Military Applications
In military and defense systems, there’s no room for error. Components, especially electronic components, are subjected to intense stress, temperature swings, and high vibration. Whether embedded in avionics, communications equipment, or weapons systems, the precision of metal parts directly impacts national security and mission outcomes.
Military-grade metal parts must:
- Maintain performance in extreme conditions — heat, pressure, vibration, and corrosion
- Meet rigorous specifications, including MIL-SPEC, which defines material properties, tolerances, and durability
- Pass inspection for AS9100 and ITAR compliance, ensuring consistent quality and secure supply chain control
Only advanced manufacturing methods, like photochemical etching — capable of producing tight tolerances, complex geometries, and consistent repeatability — can deliver the flexibility and precision to meet these demands.
Challenges in Military and Defense Manufacturing
The defense and military manufacturing industries are amongst the most challenging in the engineering world. In a military environment, components must perform under extreme duress and cannot afford even a fraction of deviation from their intended function.
Key challenges include:
Extreme Operating Environments
In defense and military applications, components are regularly subjected to extreme operating environments that demand exceptional durability and performance. These components must endure high temperatures, intense pressure, saltwater exposure, corrosive chemicals, and powerful impact forces.
To ensure long-term reliability in such harsh conditions, materials must be carefully selected and precisely processed to resist these stressors while maintaining their mechanical integrity. This level of resilience is critical for mission success and equipment longevity in the field.
Tight Tolerances and Complex Geometries
Defense and military components often demand micron-level tolerances and highly intricate geometries — features critical for applications such as miniaturized electronics, precision targeting systems, and advanced shielding solutions. Achieving this level of detail and consistency is challenging with conventional methods like machining or stamping, which struggle to deliver the precision required without compromising quality. In these high-stakes environments, even the slightest deviation can affect performance, making tight tolerances and complex designs essential for mission success.
Regulatory Compliance
In defense and military manufacturing, regulatory compliance is non-negotiable. Components must meet strict standards such as MIL-SPEC, AS9100, and ITAR to ensure reliability, safety, and national security. Documented traceability, rigorous quality control, and consistent repeatability are essential not only for meeting these requirements but also for gaining and maintaining approval as a trusted supplier within the defense supply chain.
Limitations of Traditional Manufacturing
Traditional manufacturing methods like CNC machining, stamping, and laser cutting can present significant challenges when producing components for defense and military applications. These techniques often introduce mechanical stress, warping, or distortion, which can compromise the performance and reliability of critical parts.
These processes also tend to generate excessive material waste, incur high tooling costs, and impose design limitations that hinder innovation and slow down time to market. For mission-critical components, these drawbacks can be costly and restrictive.
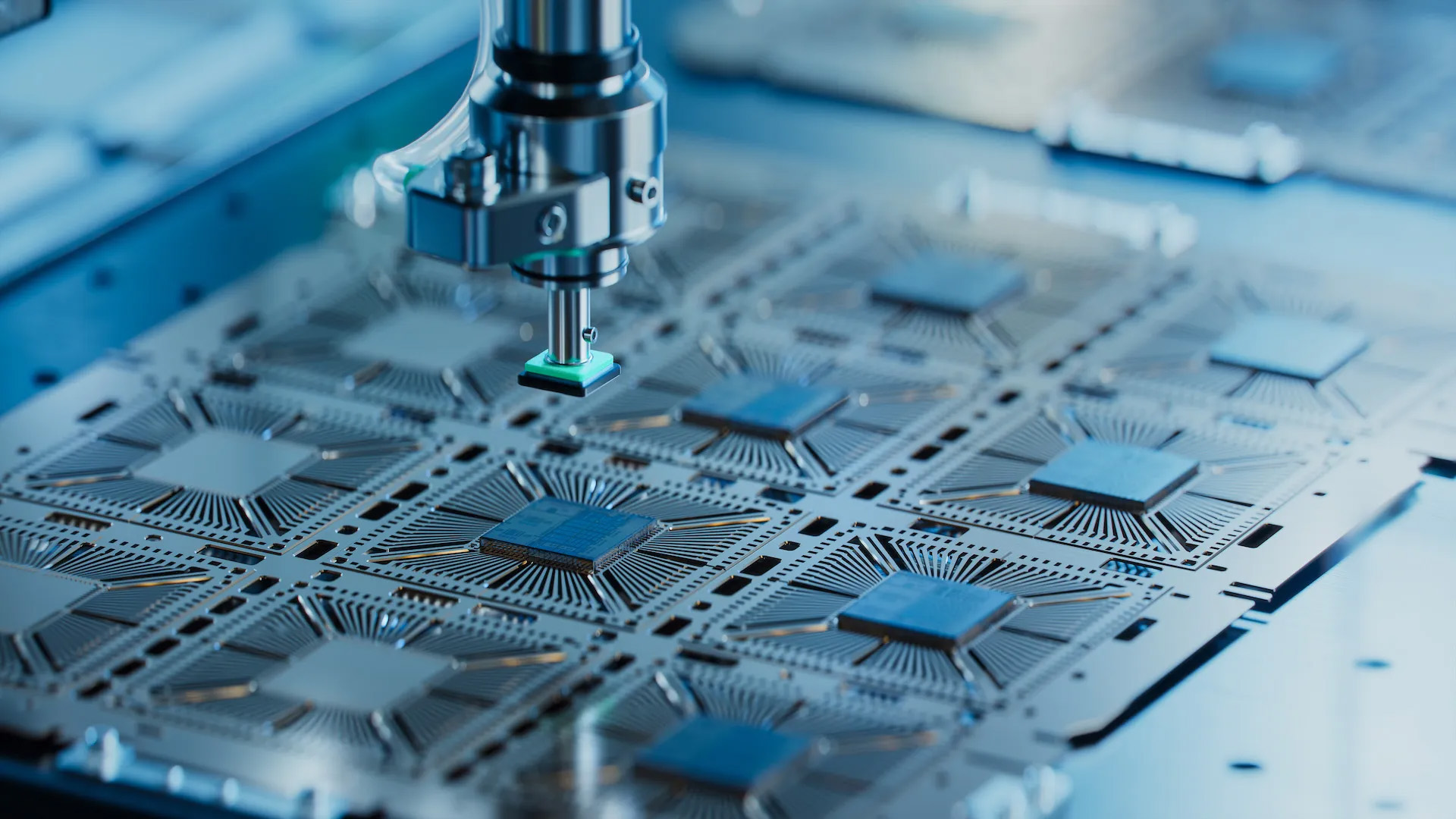
How Precision Chemical Machining Meets Military Standards
Photochemical etching (PCE), also known as photochemical machining (PCM), is a subtractive manufacturing process that uses chemical etchants and photoresist masks to create intricate metal components with extreme accuracy—without mechanical force or heat.
Why PCE is Ideal for Military Manufacturing:
Photochemical etching (PCE) is ideal for military manufacturing thanks to its unique ability to produce highly precise, burr-free components without altering the metal’s properties, which is essential for optimal performance in challenging defense conditions.
The innovative process also allows for complex geometries and tight tolerances, all while supporting a wide range of high-performance alloys. The flexibility, speed, and scalability it offers make it the perfect process for both prototyping and full-scale production of mission-critical parts.
Some of the key advantages of PCE include:
- Unmatched Precision: PCE achieves ultra-fine features with tolerances as tight as ±0.0005” (0.0127mm), crucial for modern defense systems
- No Mechanical Stress: Unlike laser cutting or stamping, PCE doesn’t stress the material, preserving its full strength and stability
- Complexity Without Cost: Complex shapes, holes, cutouts, and patterns can be produced with no increase in tooling cost—a major advantage over conventional processes
- Rapid Prototyping to Full Production: Because PCE requires only digital tooling (photo masks), PEI can move quickly from prototype to production
- MIL-SPEC, AS9100 & ITAR Compliance: PEI’s etching technology meets all regulatory and quality assurance standards required by the defense sector
PEI routinely produces parts from 0.0005 in. (0.0127mm) to 0.1250 in. (3.175mm) thick, including precision shims used by defense and aerospace contractors to level or balance systems like missiles, optics, avionics, and satellite assemblies.
Material Selection for Military-Grade Precision Parts
In defense manufacturing, material selection is critical to ensuring that components perform reliably under extreme conditions, including high stress, temperature fluctuations, and corrosive environments.
The right material not only enhances strength and durability but also contributes to weight reduction, corrosion resistance, and overall system efficiency. A carefully chosen material can be the difference between mission success and catastrophic failure.
The most common materials used for components in defense manufacturing include:
- Stainless Steel: Excellent corrosion resistance and strength
- Titanium: Lightweight with superior strength-to-weight ratio; ideal for aerospace
- Beryllium Copper: High conductivity and fatigue strength, often used in electrical contacts and RF shielding
- Nickel Alloys: Exceptional resistance to heat and oxidation
- Molybdenum: High melting point, low thermal expansion — ideal for high-temp defense systems
- Nickel Silver: Great for soldering and forming, with stable electrical properties
PEI’s material selection expertise allows us to match the optimal material to your performance requirements, whether for satellite components or battlefield electronics. Our teams understand the benefits of every metal and are ready to help refine engineering plans for maximum effectiveness.
We can source nearly any material thanks to our relationships with The Partner Companies and our advanced manufacturing partners.
Applications of Precision Metal Parts in Military and Defense
Precision metal components are used across virtually every defense platform — from land vehicles and aircraft to electronic warfare systems and unmanned drones.
Here are a few key application areas:
Aerospace & Avionics
- Radar systems and satellite communications demand aerospace components with tight tolerances and low-weight
- Aircraft instrumentation benefits from vibration-resistant, lightweight metal parts
- Etched components contribute to weight reduction, increasing fuel efficiency and performance
Weapons Systems
- Precision parts are used in firing mechanisms, missile guidance, and targeting assemblies
- Shims, brackets, and metal gaskets provide exact alignment and isolation for mission-critical functions
Electronic Warfare & Communications
- EMI/RFI shielding is crucial for secure, uninterrupted data transmission
- PEI’s etched RF shields provide protection without adding weight or limiting accessibility
- Heat exchangers and cooling plates help manage thermal loads in high-frequency electronics
Defense Vehicles & Equipment
- Etched components are found in ground vehicles, naval ships, and aerial drones
- Lightweight, high-strength parts improve maneuverability, payload, and fuel efficiency
- Custom metal filters, screens, and housings provide rugged, field-tested durability
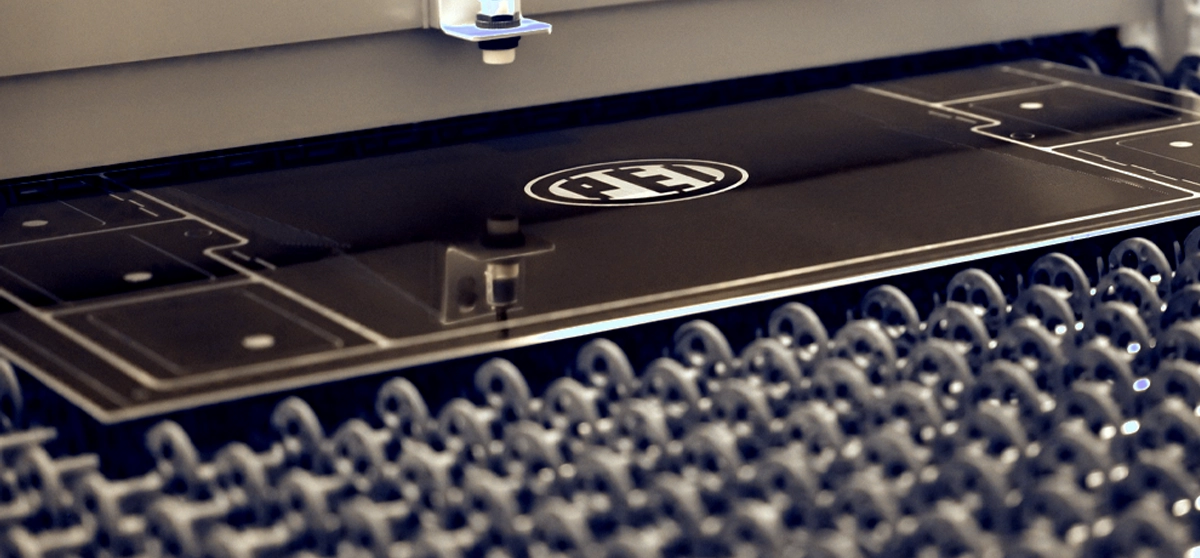
The Proven Partner for Serving the Defense and Aerospace Sector
PEI is not just a manufacturer—we’re a trusted resource for mission-critical metal components used by the world’s leading defense and aerospace OEMs. For over 50 years, we’ve stood shoulder to shoulder as leading companies push forward with revolutionary changes that change the world.
- AS9100 & ITAR Certified: Our facilities and processes meet the strictest quality and regulatory standards
- Proven Track Record: Our components can be found in hundreds of defense programs — from satellite assemblies to battlefield communication systems
- Scalable Solutions: Whether you’re building a prototype or scaling to full production, we deliver consistent, high-quality parts with speed and accuracy. From prototype to high-volume production, our team can do it all.
- Precision Chemical Etching: Our manufacturing operators have a 50-plus-year history of producing accurate, durable, and dependable metal parts via precision chemical machining (PCM).
- Custom EMI/RFI Shields: Our patented shield cans feature a removable cover for easy internal component access, simplifying maintenance and upgrades without damage to surrounding parts
We continue to partner with leaders in defense and aerospace manufacturing, offering unmatched expertise in photochemical machining, photo etched parts, and thin-metal part production.
Work with Experts in Defense and Aerospace Manufacturing
Precision metal parts are the unsung heroes of military and defense technology. From shielding sensitive electronics to stabilizing missile systems, their role is essential to performance, safety, and national security.
Unlike traditional manufacturing methods, photochemical etching offers superior accuracy, complexity, and material integrity without excessive cost or delay. Whether for prototyping or full-scale production, this innovative manufacturing process enables the creation of highly detailed, durable components that meet the exacting standards of the military and defense sectors.
For over 50 years, the expert team at PEI has built its reputation on delivering high-precision, mission-ready metal parts to those who need them most. With a certified, state-of-the-art facility, decades of experience, and a team of passionate experts, we’ve become the trusted partner for photo etching for the defense, military, and aerospace industries. Proven masters of metal etching, we’re a leading manufacturer of precision photo-etched components that are powering mission-critical systems right across the globe.
Whether you work in the defense, military, or aerospace industry, we’re ready to partner with you on your most critical challenges.
Contact us today, and let’s discuss your project!